From iPhone ear scan to printed 3D device in under 60 minutes...Down Under
3D
An Australian university-based start-up is ready to market a one-hour 3D printing service for personalised hearing device shapes, and it uses iPhone scanning to provide the mould data.
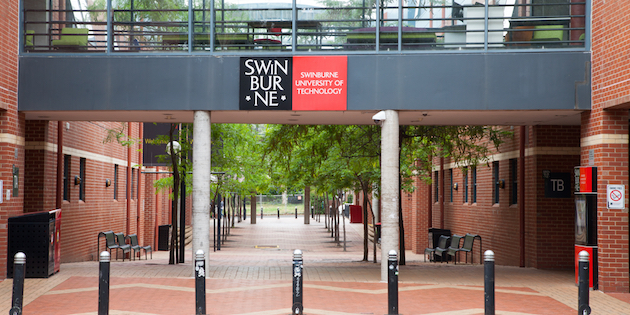
The project using this ultra-fast turnaround is led by Melbourne's Swinburne University of Technology, which has advanced experience in 3D applications in many fields and on an industrial scale.
Ear moulds traditionally take days to make, but the process developed by this project—Hearables 3D—starts off by scanning through an iPhone and proprietary software, then processing this data to produce a finished product in under one hour. This advanced 3D printing tech serves for both earphones and hearing aids.
Chief Operating Officer (COO) and co-founder of Hearables 3D, Damian Png, said: “We all know someone who carries the burden of earphones falling out or being uncomfortable. For those who wear hearing aids all day every day, a poorly fitted device isn't just uncomfortable, it becomes painful. So much so that they're willing to give up one of their five senses.”
The start-up is now moving ahead with commercialisation of the system.
Source: Swinburne University of Technology